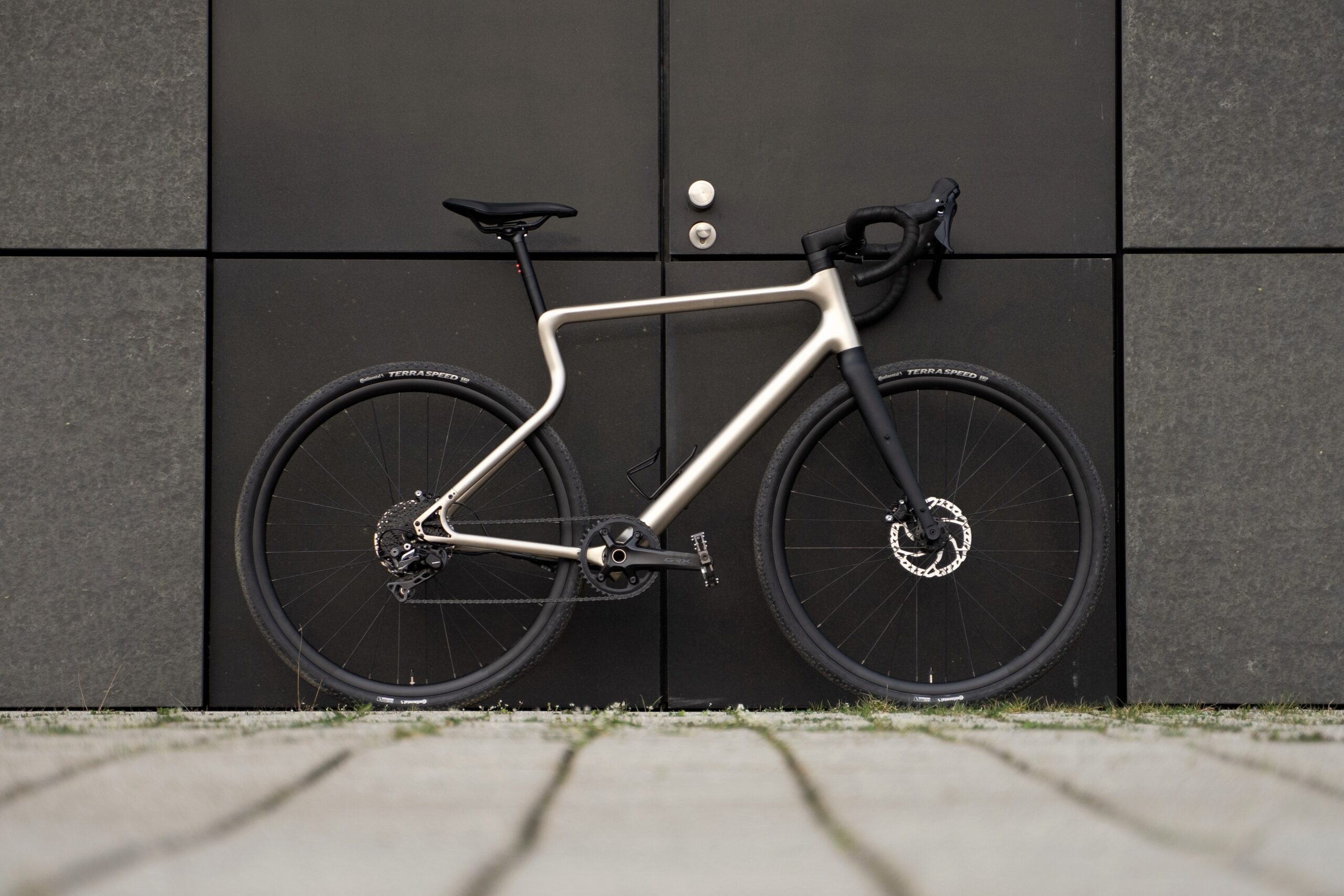
Exploring the Creative Process of URWAHN Bikes and Their Award-Winning E-Gravel Bike
April 24, 2023We are thrilled to bring you an interview with URWAHN Bikes, the proud recipient of the FIT Sport Design Award for their Waldwiesel E-Gravel Bike. URWAHN is a company that is committed to sustainability, fairness, and functionality when it comes to premium mobility, with a strong emphasis on the environment and people. With their efficient use of materials and interdisciplinary approach to product development, they have created some of the most innovative e-bikes on the market. In this interview, we will delve into URWAHN’s vision, culture, and creative process, as well as the challenges they faced while developing their cutting-edge 3D-printed gravel e-bike.
URWAHN has been creating uncompromisingly fair and functional premium mobility since 2013. We act human-centred – the focus of our actions is the human being with a fascination for elegance, concentrated performance and pure driving pleasure. With Integrated Design Engineering, URWAHN creates an interdisciplinary approach to product development that breaks with old thought patterns. URWAHN uses efficient materials, design and development processes and disrupts them in a holistic approach. Originality meets urban needs, established values meet optimisation mania. Designing our own cosmos, a habitat between city and country, between asphalt and gravel. We create mobility in the now on the way to tomorrow.
URWAHN is responsible for designing urban mobility in an interdisciplinary approach with a focus on people and our environment. The cities of our time are bursting at the seams and crying out for new mobility solutions for a better quality of life while at the same time protecting the ecosystem. With our customised URWAHN e-bikes, we create an attractive means of transport that technically takes into account the needs of use in an urban environment and adapts individually to the user. In doing so, we attach great importance to resource-saving value creation in a regional setting, which sustainably enhances the already green image of cycling.
Since its foundation, URWAHN has pursued unconventional goals that are rarely found in the industry. We live true sustainability and are committed to human-centred product development with demand-oriented value creation in the regional environment. Using 3D printing, we have succeeded in locating the series production of our premium e-bikes entirely in Germany. We already produce our innovative Softride frame in our ecosystem and are now transferring the multitude of add-on parts to our home country. Our production network is consistent, fair, eye-to-eye and largely takes place in a closed loop. We think outside the box and have created the most sustainable mobility – URWAHN e-bikes.
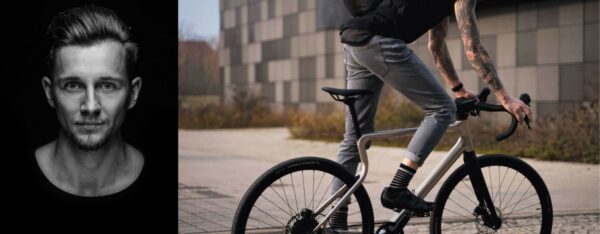
Sebastian Meinecke, CEO and designer behind URWAHN / Waldwiesel E-Gravel Bike.
Could you tell us about the company’s culture and philosophy, and how these values influence your product development and design process?
Our guiding principles form the basic framework for a sustainable and high-tech network of regional stakeholders. We are a young and dynamic team that relies on flat hierarchies, holocratic work structures and state-of-the-art processes and procedural models. Interdisciplinarily complemented by a multitude of qualitative industry and cooperation partners, we combine product development, manufacturing and production as well as business field development under one roof.
People and nature are just as important to us as aesthetic design, and consequently form the foundation for holistic development and the processes that follow. Through the regional anchoring of our value chain, we also create a profound transparency characterised by a fair wage policy and appropriate working conditions for all actors involved in development and production.
Could you walk us through the creative process involved in developing a 3D-printed gravel e-bike?
We have brought production back to Germany and created an ecosystem with well over 20 selected industrial partners. Together, we produce at eye level and set new standards in process and manufacturing quality. Our sophisticated supply chains are aligned with the principles of lean and quick response manufacturing, which enables us to guarantee demand-driven and sustainable closed-loop production. Metallurgical 3D printing plays the central role and forms the disruptive breeding ground on which all our innovations, flexibilities, folds and dilutions are based. Through the logical and digital interlinking of our value creation processes, we can also save valuable resources and act more sustainably in a holistic approach.
The most interesting and innovative process is the 3d-printing process itself: The highly complex and thin-walled connecting elements form the heart of the Softride steel frame and significantly shape its innovative character. With the help of metallurgical 3D printing, the unmistakable free forms are created in the most modern production environment and in application of the LPBF process (Laser Powder Bed Fusion). The laser melting technology (Selective Laser Melting) is used, which allows each component to be created three-dimensionally in a powder bed of high-strength steel in a layered construction. With 3D printing technology, we can drastically shorten the manufacturing process, align it according to requirements and even save on cost-intensive tools in favour of economic efficiency. The fact that there are virtually no limits to the component geometry and that 100% of the materials can be returned to the cycle are further highlights of regional 3D printing.
Our advanced frame design acts holistically in the service of use and our environment characterised by a modular, timeless yet distinctive signature. Technological innovation forms the functional basis for achieving smart mobility in a human-centred way. Through the use of pioneering technologies, we bring value creation back to the place of purpose and lay the foundation for demand-driven development and production. This is the most important core that we focus on in our development.
What were some of the key design and engineering challenges that you faced during the development of the e-bike, and how did you overcome them?
In principle, each development step is accompanied by specific difficulties. The development and later certification of the frame presented Sebastian with extensive design issues that were overcome through numerous prototype tests, simulations or optimisation loops. Finding a suitable uncompromising production process was also associated with great difficulties because we as a company could not build on any foundation. The 3D printing process was not used in the bicycle industry at the time and even today other bicycle manufacturers only produce prototypes or individual parts in small series. (Exception: Bastion Cycles from Australia). The perseverance and financial security of the project and the personal upkeep presented us with challenges again and again in the course of the project. The state of Saxony-Anhalt has created an excellent funding landscape for innovative companies, which unfortunately has been used by far too few. We have benefited greatly from this. It is also thanks to our investors that we are now able to shake up the bicycle market with our e-bikes.
The Waldwiesel boasts impressive performance metrics, such as a range of up to 80km and a weight of only 14.8kg. Could you elaborate on the design features and technological innovations that enabled these achievements?
One of the core features is the URWAHN steel frame that was constructed to meet such weight and performance targets. For example, the Softride structure ensures a high level of comfort in the rough urban jungle. Here, the rear triangle is elastically suspended and effectively compensates for unevenness. The highly innovative 3D steel printing process allows for a light-footed, robust and above all resource-saving platform construction. The precise electric drive with 40 Nm of torque at the rear wheel brings you to your destination even faster and, above all, with more pleasure. The battery is positively integrated into the down tube and supports you for up to 80 km. The drive can be connected smartly via app. The form-fittingly integrated and self-sufficiently powered LED system lets you steer the Fox safely through the night. An integrated GPS tracking system always tells you where your bike is and protects you in case of theft.
How do you position the Waldwiesel in the context of sustainable sports gear, and what steps have URWAHN Bikes taken to minimize its environmental impact and promote eco-friendly cycling?
URWAHN has been at odds with the machinations of its own industry since its foundation. True to the motto “higher, faster, further”, a large part of the competition is moving further and further away from the needs of the users, completely overshadowing the environment in the process. We pursue other goals and are committed to human-centred product development with demand-oriented value creation in the regional environment. For us, it is of fundamental importance to leave the comfort zone and score with real values. With the help of 3D printing, we have succeeded in setting up series production centrally in Germany. We already produce our innovative Softride frame entirely in Germany and are now transferring the multitude of add-on parts into our specially created ecosystem. In this ecosystem, we cooperate fairly and on an equal footing with all our partners and even go one step further: the majority of our production chains work in a closed cycle. In this way, we can breathe a second life into worn-out e-bikes and all add-on parts through refurbishment and recycling processes.
URWAHN is doing pioneering work and has deeply anchored the topic of sustainability at all levels of the company. The “FairFrame” label is only the tip of the scales and a symbol for all those activities that should have long been obligatory in the present. We think outside the box and have created what is probably the most sustainable mobility – URWAHN e-bikes.
Our Softride frame proves to be a venerable material pioneer. By using original materials such as steel, we can close the cycle of our value creation and conserve valuable resources. Steel guarantees strength and stiffness and is much easier to process than aluminum and carbon. This means that we can use the best manufacturing techniques from an ecological and environmental point of view and give steel completely new applications in terms of form and function. In addition, we can completely repair, reprocess and recycle steel, which enables us to close the cycle and drastically increase the service life of the material. Steel rethought!
As a company, we have a significant influence on people’s mobility and behaviour with our products. Our premium e-bikes are puristic in appearance, functionally innovative and, at their core, completely recyclable, i.e. adaptable and repairable at any time. However, we bear responsibility not only for the use of our premium e-bikes, but also for the production and for all actors involved in the value creation. It is not without reason that we have centralised our production in Germany and guarantee complete product and process transparency to our shareholders and stakeholders at all times. All our stakeholders are paid fairly by us and are in appropriate working environments with holocratic structures. We try to live up to our responsibility at all levels, we undergo external audits and also try to proactively encourage our industry to act more responsibly within the framework of our “FairFrame” label.
Congratulations on winning the FIT Award for Sport Equipment Design! How does it feel to receive such recognition, and how does it inspire your team to continue pushing the boundaries of bike design and innovation?
Thank you very much for the Award. It’s a great recognition for the team and all people being part of the URWAHN adventure. We have met fantastic people who have been with us on our journey to an extraordinary bike. So, it’s also an honor for all participants and the team behind URWAHN. We have never thought about coming so far. Thus, we feel very happy and honored about this award.
Looking ahead, how do you envision the future of e-bikes and outdoor mobility, and what trends and challenges do you anticipate in the coming years?
URWAHN is responsible for designing urban mobility in an interdisciplinary approach with a focus on people and our environment. The cities of our time are bursting at the seams and crying out for new mobility solutions for a better quality of life while at the same time protecting the ecosystem. With our customised URWAHN e-bikes, we create an attractive means of transport that technically takes into account the needs of use in an urban environment and adapts individually to the user.
URWAHN E-bikes are the key to sustainable mobility. If all our EU countries would follow the modal split of Denmark, we could already meet the climate targets set for 2025 to reduce global warming by 12-28%. And this is where all our efforts come in. We are on a sustainable mission and put people and the environment at the center of everything we do for a reason. It is our duty to take the requirements and needs for use seriously, tailor them and bundle them into an attractive overall solution. Only in this way do we bring ourselves back into harmonious balance with our nature.
URWAHN is thus an integral part of the mobility turnaround and creates unprecedented e-bikes that symbiotically seduce people into environmentally conscious locomotion – for more freedom and space, for less traffic density and stress, for more movement and health, for less Co2 and more green spaces.
Finally, can you give us a sneak peek into any upcoming projects or developments that URWAHN Bikes is working on?
URWAHN is a technology pioneer and world market leader in the series production of 3D-printed premium e-bikes. Using metallurgical 3D printing, we have succeeded in bringing production back to Germany. We will pick up where we left off and put more frame geometries on the asphalt. We are also experimenting with other materials that make further advantages in terms of lightness and flexibility possible. So, on the material level, we can still get a lot out of 3D printing. In addition, we will also continue to develop the technical components and shifting types. A bit vague, but we want to keep the excitement high.